Magnetic Gripper for Car Frame Welding
Robot arms play a significant role in car frame welding. They automate the welding process, reducing the need for manual labor and increasing productivity. In this article, we are going to discuss an efficient end-of-arm tooling in car frame welding: magnetic gripper.
What is car frame welding
Car frame welding is a crucial process in automotive manufacturing. It involves joining different parts of the car frame together using welding techniques. Welding creates a strong bond between metal components, ensuring the structural integrity and safety of the vehicle.
Advantages of magnetic gripper over mechanical gripper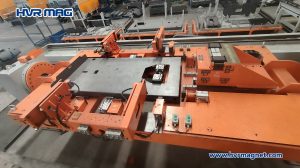
Workpiece positioning: Multiple magnetic grippers can be operated to fix synchronously with one key, avoiding workpiece deformation or displacement.
Clamping and stability: Magnetic gripper holds workpieces in place from the back by strong magnetic field, which prevents the surface of the workpiece from being pinched or deformed.
Accessibility and maneuverability: Magnetic grippers do not obstruct the welding process with the welding gun because it attracts the workpiece from the back, making the welding smoother.
Changes after using magnetic gripper instead of mechanical gripper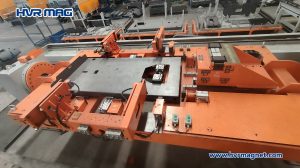
This client customized a group of magnetic grippers. The car frame welding group adopts various types of electro permanent magnets, controlled by several sets of electro permanent magnetic controllers, which can meet the different specification frame set welding in length from 5 to 12 meters.
Magnetic gripper significantly improved productivity, with capacity more than three times higher than before. Welding process becomes smoother and product defective rate reduces. Labor costs are also reduced, from 3-4 people to unmanned operations.
For more information, please contact HVR MAG at export@hvrmagnet.com