About the Electro-permanent Magnet Technology: Guide
Electro-permanent magnet technology emerged in the 1980s and then has been popularized in foreign countries. The domestic market has only grown rapidly in the last decade or so. Today let’s learn some basic knowledge about EPM technology.
What is the working principle of the electro-permanent magnet (EPM)?
As the name applies, Electro-Permanent Magnet is a hybrid of electro lifting magnet and permanent magnet. And during the working process, it can maintain the magnetic force without electricity. Because the magnetic force only relies on the permanent magnet inside. And it uses electricity to activate and deactivate the magnet power only. It is small in size and has a strong magnetic force of 16kg/CM2. That’s why it is popular in the international market.
What is the difference between electro-permanent magnets and permanent magnets?
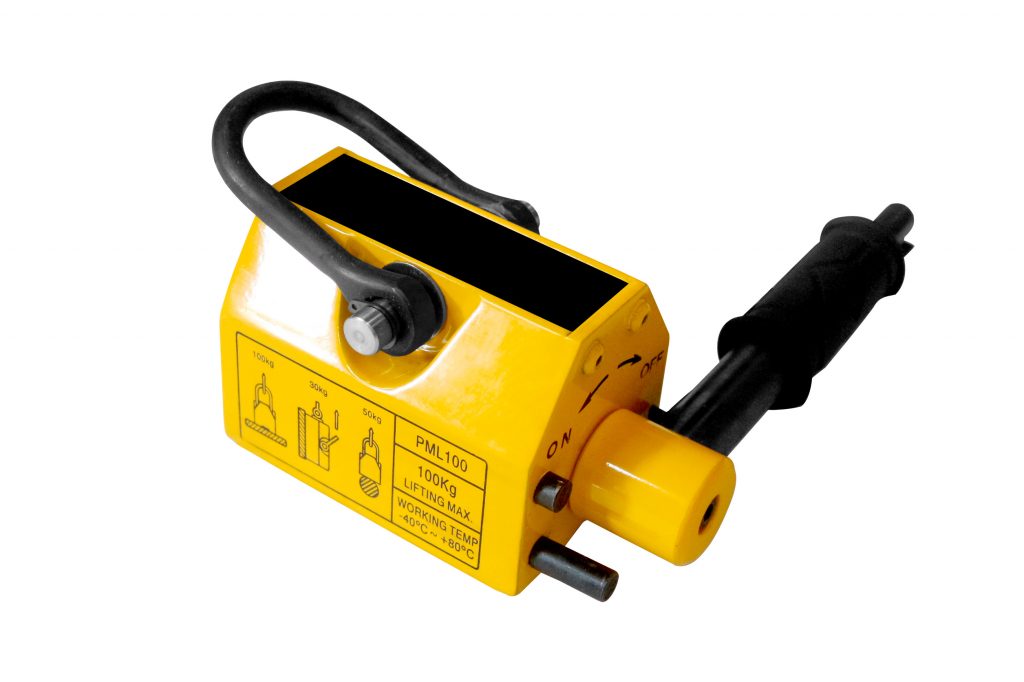
The electro-permanent magnet relies on the instantaneous current to switch the magnetic field polarity. This process is externally characterized as the magnetizing state and demagnetizing state. While the permanent magnet relies on manual or mechanical transmission to switch the magnetic field polarity. Besides, the electro-permanent magnet has adjustable magnetic permeability depth, better synchronization, remote control operation, simpler operation, and no internal moving parts.
How long can the magnetism of the EPM be maintained in case of a power failure?
The electro-permanent magnet is made of permanent magnetic material, hence the magnetic source part does not rely on electric power. The magnetic force will not decay as time goes by (if the working environment keeps the same). In case of a blackout, as long as after the magnet is magnetized, the workpiece will always keep adsorbed. And it will not fall off even for 10 years under the power failure.
What are the main application fields of electro-permanent magnet technology?
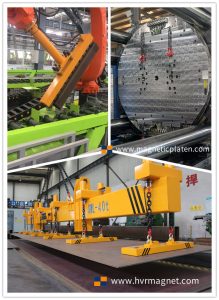
1. Lifting magnet. It is widely used in steel structural fabrication, shipbuilding, dock, logistics, warehousing, metalworking, etc. Compared with steel clamps, hooks, and wires, custom-made lifting magnets have incomparable advantages. They are more efficient, and safer, and they have a longer service life and near-zero maintenance.
2. Robotic arm grippers. HVR MAG manufacturers magnetic grippers applied to industrial robots for automated material handling. Magnetic grippers are for material loading and unloading, palletizing and depalletizing, sorting, welding fixture, etc. Its market occupation has grown quickly in recent years.
3. Quick mold change system. HVR MAG manufactures magnetic platens for injection molding machines to clamp the mold. It can largely reduce the mold change cycle and improve productivity and the factory layout environment.
4. Electro-permanent magnetic chucks are applied in the machinery manufacturing industry mainly. They are suitable for grinding machine processing, lathe machine processing, and other high-precision CNC center.
From being one of the first electro-permanent magnet manufacturers in China to our cutting-edge magnetic solution capabilities, HVR MAG is a very specialized and professional brand of electro-permanent magnet technology. Its major products include magnetic lifters, grippers, and magnetic quick mold change solutions. If you are interested, please e-mail us at: export@hvrmagnet.com