How to Choose an Industrial Pump
Selecting the right industrial pump ensures efficient and reliable fluid handling in various industrial applications. Whether you are involved in manufacturing, construction, mining or wastewater treatment, choosing the appropriate pump can optimize performance, minimize downtime and reduce operational costs.
You’ll want to consider factors such as application requirements, fluid properties, flow rates and system parameters to make an informed decision. Learn how to choose a pump in this informative guide.
Main Types of Industrial Pumps and Their Applications and Benefits
When looking at which industrial pump is best, it comes down to your requirements. Industrial pumps are a complex component in numerous applications, ranging from manufacturing processes to wastewater treatment. The following industrial pump types are the main ones commonly used:
Centrifugal Pumps
Centrifugal pumps work on the principle of centrifugal force, using an impeller to propel fluids through the pump’s casing. Centrifugal pumps are highly efficient in handling large volumes of liquids with low to moderate viscosity. They are used for water transfer, chemical processing, irrigation and HVAC systems.
The benefits of centrifugal pumps include:
High flow rates: Centrifugal pumps can move substantial amounts of liquid, making them suitable for large-scale operations.
Wide range of head capabilities: These pumps can handle a broad spectrum of pressure requirements, ensuring flexibility across various applications.
Easy maintenance: With a simple design and fewer moving parts, centrifugal pumps are relatively easy to maintain, resulting in reduced downtime and lower maintenance costs.
Self-Priming Pumps
Self-priming pumps automatically remove air or gas from the suction line, allowing them to operate even when the liquid source is below the pump’s level. This feature eliminates manual priming and makes self-priming pumps suitable for applications where the pump may encounter air pockets or intermittent flow conditions.
Here are some of the benefits of self-priming pumps:
Ease of use: Self-priming pumps eliminate the hassle of manual priming, reducing the time and effort required to start the pump.
Versatile application range: These pumps can handle various liquids, including water, chemicals, sludge and wastewater, making them adaptable to diverse industrial settings.
Reliable operation: Self-priming pumps maintain prime even under challenging conditions, ensuring consistent performance and minimizing downtime.
Diaphragm Pumps
Diaphragm pumps or membrane pumps are positive displacement pumps that use a flexible diaphragm to displace the fluid. These pumps handle abrasive, corrosive or viscous fluids and liquids with suspended solids.
The benefits of diaphragm pumps include:
Excellent chemical compatibility: Diaphragm pumps can handle aggressive fluids, including acids, solvents and caustic substances, without risking pump integrity.
Ability to handle solids: The diaphragm design allows these pumps to handle liquids with suspended solids, making them suitable for slurry applications or wastewater containing debris.
Versatile installation options: These pumps can be installed in various positions, including horizontal, vertical or even upside down, providing flexibility in installation and ensuring optimal space utilization in different industrial setups.
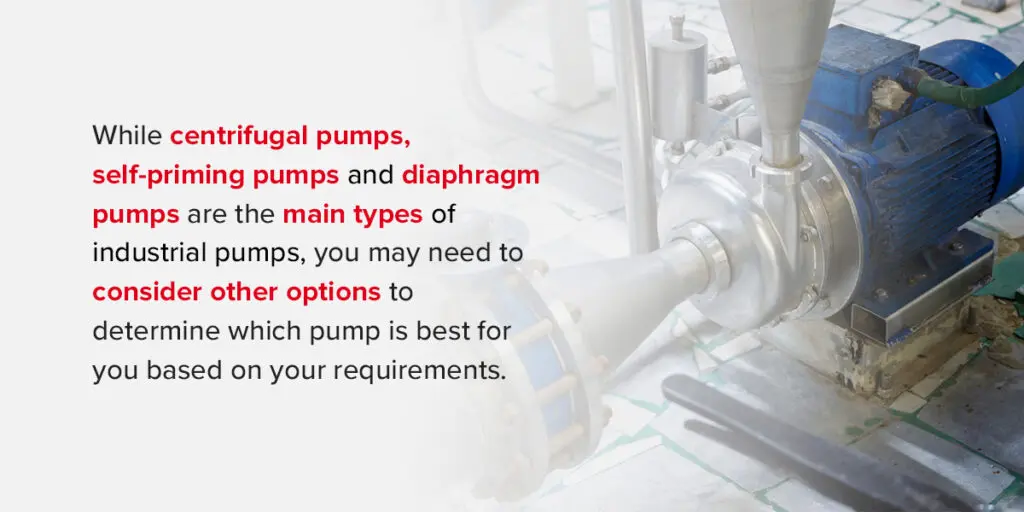